Pacific North Press is a print shop located in NE Portland, whose offerings include textile/garment screen printing, embroidery, vinyl decals, vinyl branding for walls, windows, and vehicles, as well as custom signs. Specializing in high-quality screen printing, Pacific North Press offers standard screen printing, high detail process printing, specializing in water-based and discharge inks, with a distinct approach to sourcing quality, sustainable goods with the best possible finish. Their clients span from local to national and also offers a bi-monthly screen-printing technical education through one of their supply distributors.
Success Story
Pacific Northpress
Industry
Location
Date Founded
Number of Employees
Background
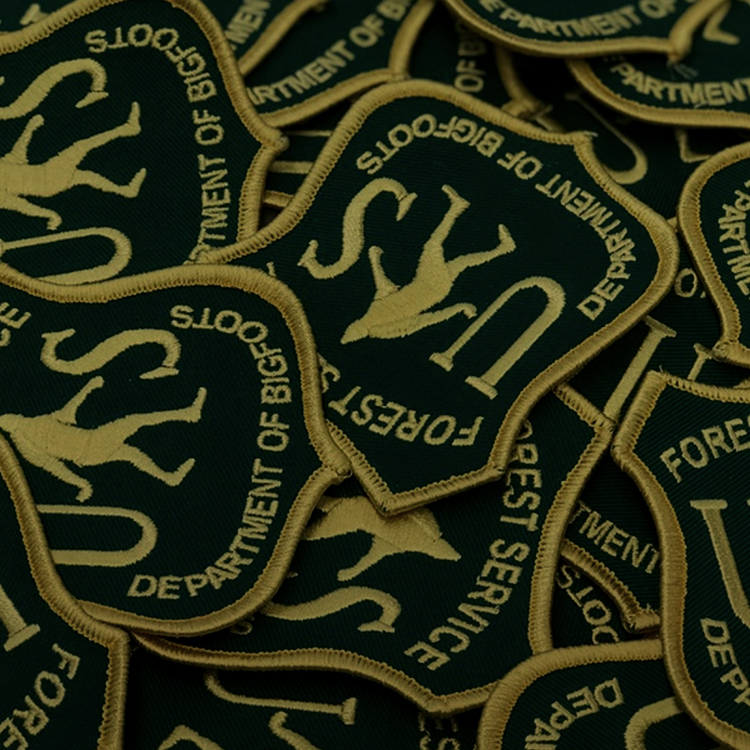
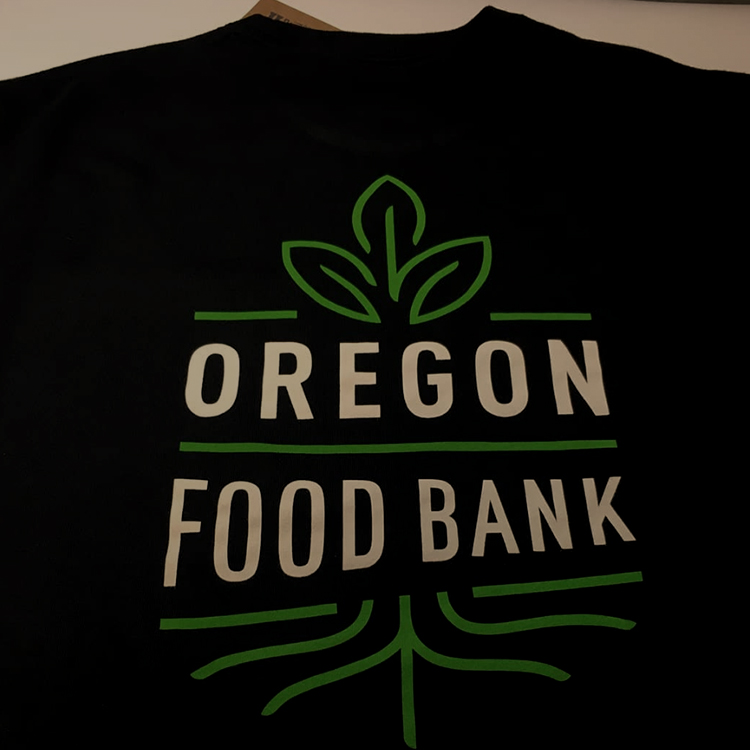
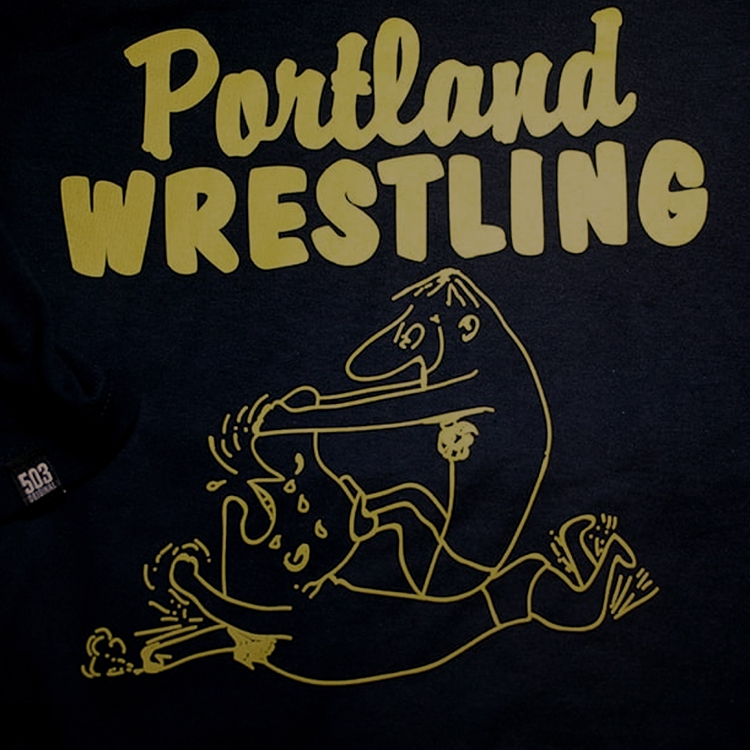
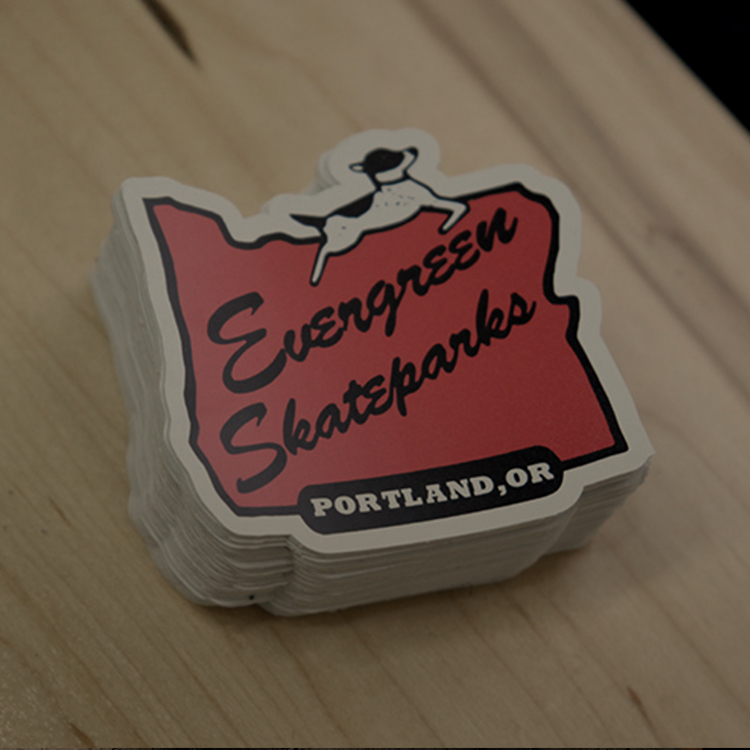
$200,000
$500,000
INCREASED CAPACITY
The Situation
The leadership team at Pacific North Press (PNP) recognized that there were more efficient ways to produce their products. PNP wanted to eliminate waste in their process and create a more focused approach. Production and business duties were managed through tribal knowledge, without formal training documentation or a clear process. This meant training time for new employees was long and capturing standard work was difficult.
PNP understood that there was room for improvement, especially because they create custom products. They wanted to create a more visual work environment where production status, the pace of work, and progress could be monitored by anyone in the organization.
The Solution
To begin, PNP participated in a Lean Fundamentals cohort to empower all team members to identify and reduce waste, differentiate between value-add and non-value-add activities and understand the principles of lean manufacturing. In collaboration with OMEP, the PNP team created a future state value stream map to help improve flow throughout the company process as a whole.
To create flow in their production process, OMEP helped PNP to implement visual scheduling, daily huddles, and an organized workspace (by implementing 5S). PNP also documented standard processes to be able to train new employees faster and defined job roles and responsibilities to set clear expectations and offer opportunities for cross-training and advancement.
The Results
By implementing the ideas in the value stream map to eliminate waste, PNP saved $200,000. They were able to increase capacity and throughput in their order processing, inventory storage, and production process, resulting in an increase of about $500,000 in sales.
Schedule Your No-Cost Assesment with OMEP Today!
SCHEDULE A VISIT
Our work with OMEP and Linda was instrumental in improving our workflow, finding inefficiencies, and leaning up our business. The insight into scaling our manufacturing proved to be both profitable and unrivaled in making our lives less stressful. We can't wait until the next round!