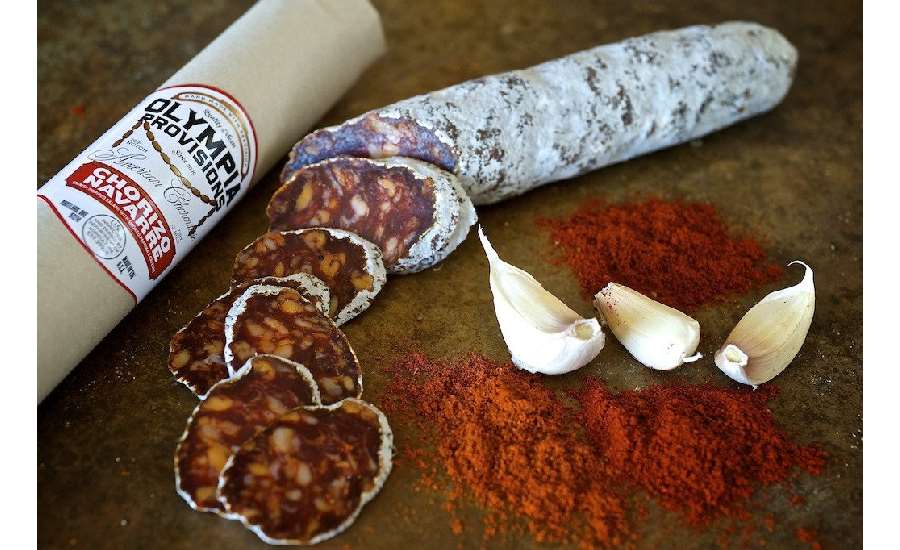
Olympia Provisions, located in Portland, Ore., was Oregon’s first USDA-approved salumeria, established in 2009. Salumist Elias Cairo grew up a first-generation Greek-American with a father who made charcuterie at home. Cairo then traveled throughout Europe and returned to Oregon, to bring together his accumulated knowledge of Old-World meat curing.
Olympia Provisions provides a wide range of specialty cured meats, including numerous varieties of salami, chorizo, sausage, pâté and much more. Since launching in 2009, the company has grown to 160 employees, five restaurant locations and two food carts. With that success came challenges. Finding employees to meet the production needs can be difficult, and so can finding the management necessary to oversee the company’s direction.
“One of the biggest challenges with rapid growth is competing priorities. Some can be opportunities and some can be shiny pennies,” says Taylor Janes, HR director at Olympia Provisions. “It’s a unique challenge to be strategic in how we prioritize business development.”
As a USDA-inspected facility, Olympia Provisions has to operate be set standards to produce wholesome products. As batch sizes grow, new products come into production and new employees come onto the floor, it can be difficult to maintain a certain level of efficiency. In the case of Olympia, it was able to find some assistance with the Oregon Manufacturing Extension Partnership. OMEP works side by side with Oregon manufacturers to build successful businesses.
“We leverage lean methodologies to provide solutions in Manufacturing Operations (quality management, supply chain, engineering, industry 4.0), Business Financials & Strategy (financials, sales process, strategic planning) and Organizational Development (organizational design, career pathways development) to be Oregon manufacturer’s source for growth and prosperity,” explains Aaron Fox, president of OMEP.
“We see small companies struggle with business stabilization and focus. Often our clients know they need to have a strategic plan, but are too busy dealing with the daily tasks of running a company to think about the future,” he adds.
The Manufacturing Extension Partnership Program is governed by NIST (National Institute of Standards and Technology), which is governed by the Department of Commerce. It has manufacturing extension partnership centers located in all 50 states and Puerto Rico. OMEP presented to Olympia Provisions about employee development and organizational alignment, which helped the company realize that the company could use a third party with outside eyes, Janes says.
“One of the things that emerged from working with Linda Wechsler, OMEP’s consultant, was that we identified a new tier of management,” Janes says. “We promoted existing staff into assistant management positions so senior management can now delegate training and other responsibilities to those assistant managers.”
The company has more than 100 training modules, primarily developed for entry-level employees. Other training modules relate to important tasks such as sanitation and chemical ratios.
“We can now hire someone with no experience and get them into highly efficient operating standard within 60 days,” Janes says. “Before, that would have taken six months at least to get to that proficiency if they stayed that long.”
OMEP works with a number of businesses in Oregon. Fox notes that the food industry has been the fastest-growing manufacturing sector in the state for the last three years.
“Meat processors face some unique challenges,” he adds. “They have the added consideration of being USDA compliant. As a result, meat processors not only have to comply with regular food safety standards, but they also have to take into consideration the USDA standards.”
For more information about all state MEP centers, visit https://www.nist.gov/mep/mep-national-network/connect-your-local-mep-center.